Trade fair highlight 20. May 2020
mQuest® Audit – software solution for mobile audits and quality checks
1 / 6

mQuest® Audit fields of application
2 / 6

mQuest® Audit infographic
3 / 6

mQuest® Audit detail view
4 / 6

mQuest® Audit overview
5 / 6

mQuest® Audit app
6 / 6
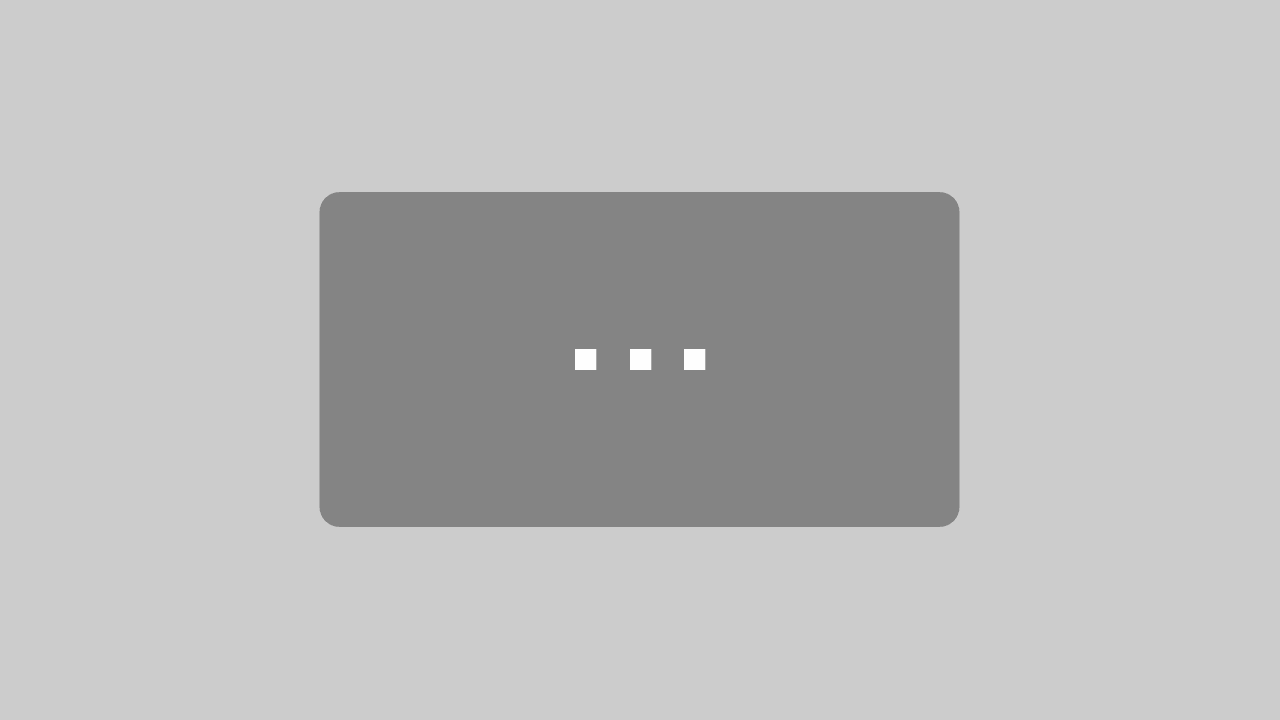
By loading the video you accept YouTube's privacy policy.
Learn more
With the smart combination of mobile offline app and web-based portal, all types of audits, like VDA 6.3, 5s, HSEQ and LPA can be digitised securely and cost-effectively. With mQuest® Audit digitisation platform cumbersome paper- and Excel-driven processes are finally obsolete.
Important KPIs are recorded mobile on the basis of checklists and forms. Planning, tracking, analysis and reporting of audits are conveniently carried out via a central, web-based portal. Obtained results provide valuable information for process optimisation, continuous quality improvement and long-term customer satisfaction.
Smart preparation and planning:
Test objects such as plants, products or processes are created and maintained in the mQuest® Audit web portal, as well as the planning of one-off or regular audits. Tailor-made checklists and forms guarantee the collection of all relevant data. Checklists can be created and edited at any time. Updates are automatically distributed to all auditors.
Mobile and independent performance:
The audits are carried out using the mQuest® Audit App and deficiencies can be recorded visually. The app runs natively on all current iOS and Android devices and is absolutely independent of WLAN or mobile phones. Collected data will bes synchronized with the system when a connection is established.
Precise and appealing evaluation:
Audits carried out are presented clearly structured in mQuest® Audit. Overviews and analyses can be easily adjusted using filters. Comprehensive analyses as well as the evaluation of a single audit are possible.
Generation and tracking of measures:
Measures for all deviations or deficiencies of an audit can be generated at the push of a button. In the management of measures, follow-up processes for the elimination of defects are planned and controlled. Responsible persons are informed about upcoming tasks and can update the status of the measure at any time.
Important KPIs are recorded mobile on the basis of checklists and forms. Planning, tracking, analysis and reporting of audits are conveniently carried out via a central, web-based portal. Obtained results provide valuable information for process optimisation, continuous quality improvement and long-term customer satisfaction.
Smart preparation and planning:
Test objects such as plants, products or processes are created and maintained in the mQuest® Audit web portal, as well as the planning of one-off or regular audits. Tailor-made checklists and forms guarantee the collection of all relevant data. Checklists can be created and edited at any time. Updates are automatically distributed to all auditors.
Mobile and independent performance:
The audits are carried out using the mQuest® Audit App and deficiencies can be recorded visually. The app runs natively on all current iOS and Android devices and is absolutely independent of WLAN or mobile phones. Collected data will bes synchronized with the system when a connection is established.
Precise and appealing evaluation:
Audits carried out are presented clearly structured in mQuest® Audit. Overviews and analyses can be easily adjusted using filters. Comprehensive analyses as well as the evaluation of a single audit are possible.
Generation and tracking of measures:
Measures for all deviations or deficiencies of an audit can be generated at the push of a button. In the management of measures, follow-up processes for the elimination of defects are planned and controlled. Responsible persons are informed about upcoming tasks and can update the status of the measure at any time.